- Menu
-
Immanquables !
-
Machines
-
Matériaux & Outils
- 3D Couleurs
- Dentaire Médical
-
- Nous Contacter
- SAV
- En savoir plus
Du scanner à l'outillage imprimé en 3D en 40 minutes
L'entreprise utilise des outils imprimés en 3D et l'impression 3D ultra-rapide de résine de bureau pour fournir des bouchons d'oreille personnalisés à ses clients.

L'utilisation de bouchons d'oreille sur mesure est recommandée par les audiologistes et les services de sécurité pour diverses raisons médicales, de protection et de confort. Les recommandations portent notamment sur la prévention des infections de l'oreille moyenne, la protection de l'audition, un meilleur ajustement des appareils auditifs, des moniteurs intra-auriculaires et des équipements de communication. Bloquer les bruits extérieurs dans les environnements de production ou pendant le sommeil, améliorer la qualité du son et protéger les oreilles contre les infections pendant la baignade sont des exemples de cas d'utilisation des bouchons d'oreille liés au confort.
Pour s'assurer que les bouchons d'oreille fonctionnent comme prévu et apportent du confort à l'utilisateur, les audiologistes et les services de sécurité recommandent que les bouchons d'oreille soient personnalisés pour s'adapter à l'individu. Le processus de personnalisation traditionnel implique qu'un audiologiste prenne l'empreinte de l'oreille en injectant de la cire dans le conduit auditif. Un fabricant prend le moule de cire et entame un processus assez long avant d'obtenir le produit final. Earfab a déjà changé la donne, grâce à des processus automatisés allant de la prise d'empreintes d'oreilles individuelles à l'aide de smartphones, à la fabrication à grande échelle - avec l'aide d'imprimantes 3D de bureau XiP ultrarapides et de machines de moulage par injection.
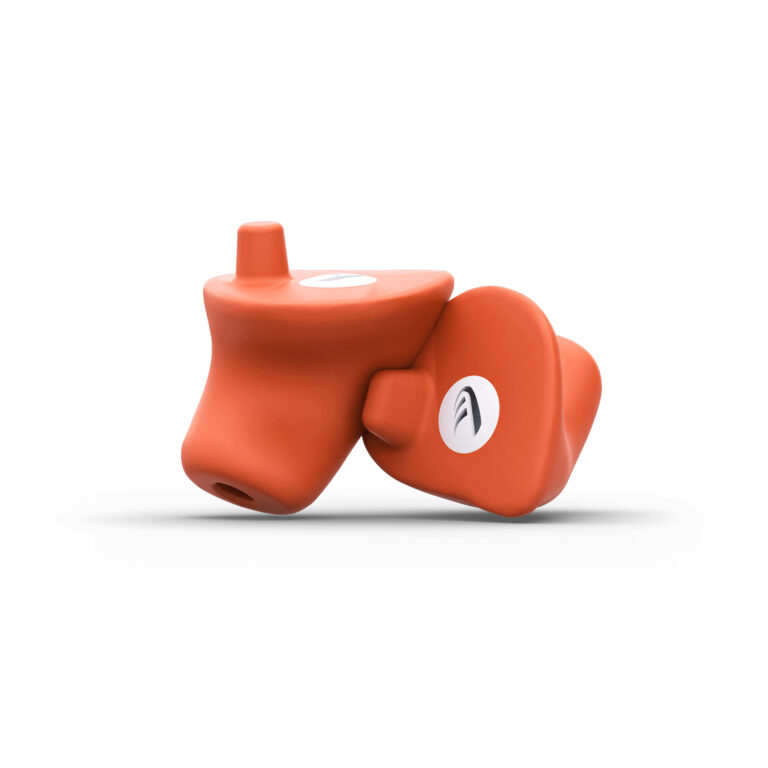
Défi
L'approche traditionnelle est trop coûteuse et prend trop de temps
Le processus conventionnel de commande de bouchons d'oreille sur mesure comporte certaines limites qui peuvent nuire à l'utilisateur, allonger les délais de production et augmenter le coût et le délai de livraison des bouchons d'oreille sur mesure. Une étude menée dans les services d'oto-rhino-laryngologie de 2 050 établissements médicaux a montré que 14,7 % d'entre eux ont subi des blessures secondaires causées par le processus physique de prise d'empreinte de l'oreille. Dans certains cas, le processus d'impression physique a laissé des résidus dans le conduit auditif, ce qui a entraîné des infections ou des blessures.
Les délais de production s'étendent de trois à huit semaines, ce qui entraîne une prolongation de la date de livraison du produit. Pour réduire considérablement le coût, la durée de production et les problèmes de santé liés aux bouchons d'oreille sur mesure, l'équipe d'earfab® a mis au point un processus entièrement numérisé afin d'optimiser la personnalisation.
"La plateforme de matériaux ouverte de XiP nous a permis d'explorer divers matériaux avant de choisir une résine biocompatible utilisée pour l'impression de notre outillage personnalisé."
Jesper Anderson, directeur général de earfab®
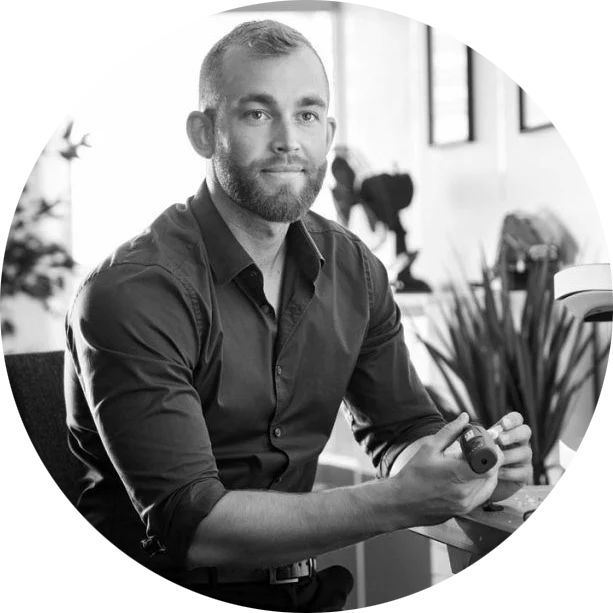
Client
earfab®
Secteur d'activité
Dispositifs médicaux / Soins de santé
Produits
■ XiP Imprimante 3D de bureau
■ Résine sur mesure Open Source
Application
■ Personnalisation avancée
■ Production finale
Avantages
■ La plateforme ouverte de XiP permet de personnaliser les profils d'impression pour les résines tierces
■ Capacité à produire 28 moules uniques et complexes en seulement 40 minutes sur une seule imprimante
■ Possibilité d'injecter des matériaux de moulage standard de qualité médicale dans un outil imprimé en 3D à l'aide d'une presse de moulage par injection conventionnelle
■ Personnalisation avancée avec un processus entièrement évolutif
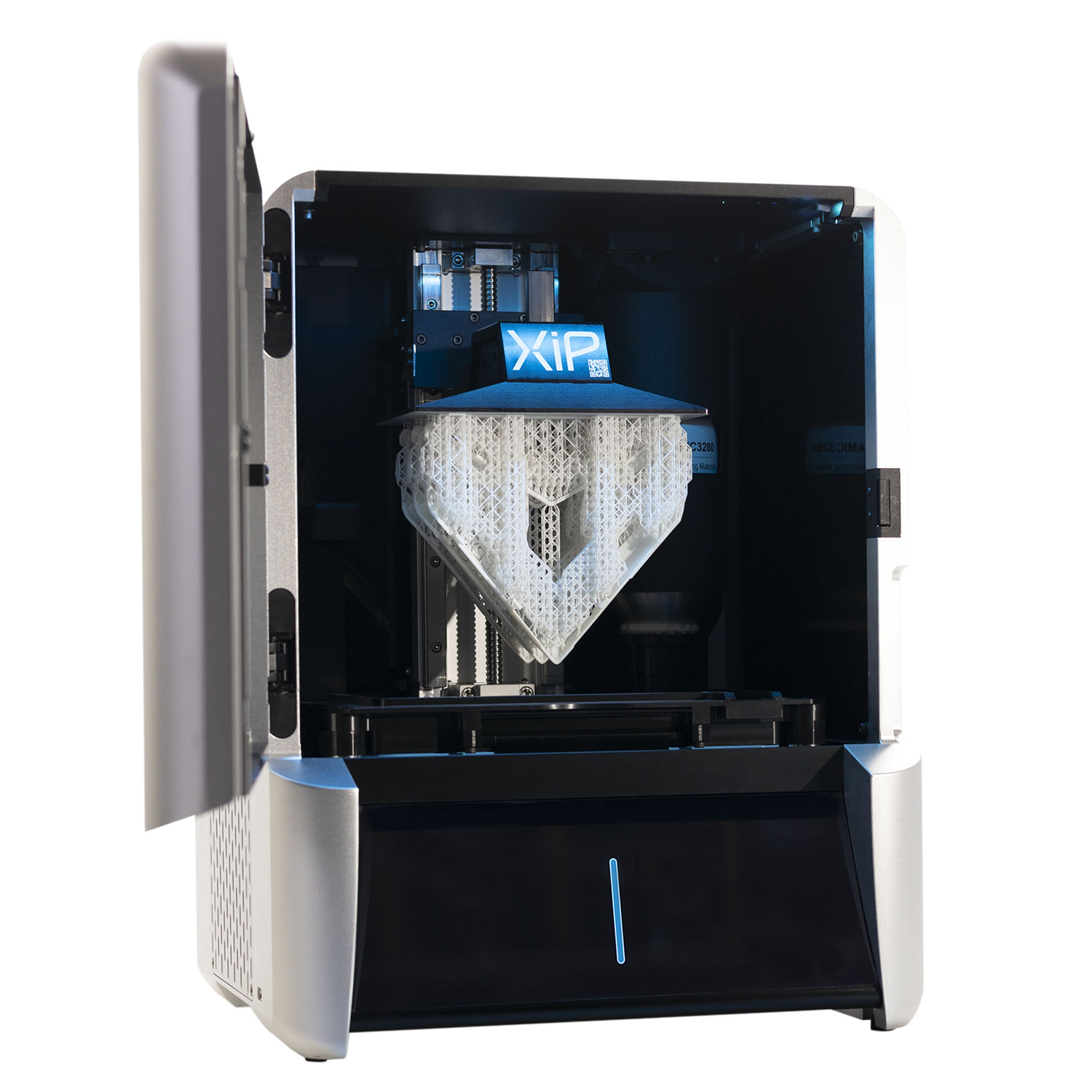
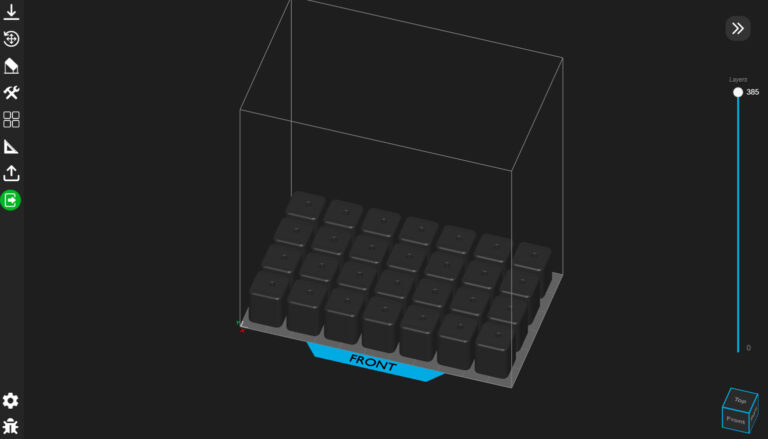
Solution
Des numérisations en 3D de l'oreille associées à l'impression 3D résine pour imprimer des outils personnalisés
Pour répondre aux défis de santé et de sécurité associés à la prise d'empreintes d'oreilles pour les produits intra-auriculaires, earfab® a lancé earfabSCAN. L'application earfabSCAN numérise le processus de prise d'empreinte de l'oreille grâce à l'application de la technologie de numérisation 3D. L'application exploite les caméras des smartphones (iPhone X Series, 11 Series et 12 Series pour l'instant - d'autres suivront plus tard en 2023). Grâce à l'application earfabSCAN, les clients capturent des scans numériques de l'oreille, y compris les géométries physiques internes de l'oreille, pour générer des empreintes numériques personnalisées de l'oreille.
La numérisation innovante du processus de prise d'empreinte de l'oreille par Earfab, grâce à l'application intuitive earfabSCAN, permet à la fois d'éliminer les défis logistiques et de réduire les coûts. Les utilisateurs finaux n'ont plus besoin de se rendre physiquement chez l'audiologiste car des empreintes précises peuvent désormais être prises dans le confort de leur domicile et, grâce à un transfert basé sur le cloud, passer directement à la fabrication dans l'un des sites de fabrication distribués par earfab.
Pour optimiser le processus de fabrication, earfab a choisi un parc d'imprimantes 3D XiP associées à une résine spécialisée pour imprimer les outils avant d'injecter leur TPE de qualité médicale. Grâce à la plateforme ouverte de l'imprimante XiP, l'équipe d'earfab® a pu qualifier la formulation de sa résine biocompatible tierce compatible avec le TPE de qualité médicale afin de produire des bouchons d'oreille sur mesure en fonction de l'anatomie spécifique du client.
"XiP travaille très rapidement, comme nous ne l'avons jamais vu sur le marché, tout en offrant des impressions de haute précision, ce qui est crucial dans le secteur des écouteurs intra-auriculaires.."
Jesper Anderson, directeur général de earfab®
Bénéfice
Personnalisation avancée et capacité de produire jusqu'à 10000 bouchons d'oreille par semaine
La numérisation de la fabrication des produits intra-auriculaires à l'aide de l'application earfabSCAN et des imprimantes 3D XiP, combinée au moulage par injection traditionnel, a permis à earfab d'augmenter avec succès sa production et de réduire ses coûts de fabrication. L'application earfabSCAN permet aux clients de prendre des empreintes d'oreilles et de les envoyer à la fabrication en seulement deux minutes. Comparé aux heures passées à se rendre chez l'audiologiste, à préparer la cire et à prendre des empreintes, le processus numérisé est transparent, rapide et sûr.
L'association d'un processus de numérisation 3D avec la fiabilité des imprimantes 3D XiP et du moulage par injection permet à earfab® d'étendre son processus de fabrication rapidement et efficacement. L'équipe prévoit de pouvoir produire jusqu'à 10 000 jeux de bouchons d'oreille personnalisés par semaine d'ici 2023 et sera en mesure d'augmenter ce nombre en cas de besoin. Le processus de numérisation permet également de réaliser des économies considérables. Aujourd'hui, la technique de fabrication sur mesure d'earfab réduit considérablement les coûts de production et les délais de livraison jusqu'à 80 %. Cela permet au client moyen d'avoir accès à des produits intra-auriculaires de haute qualité, fabriqués sur mesure, à des prix abordables et livrés en une semaine, quel que soit le nombre de commandes.
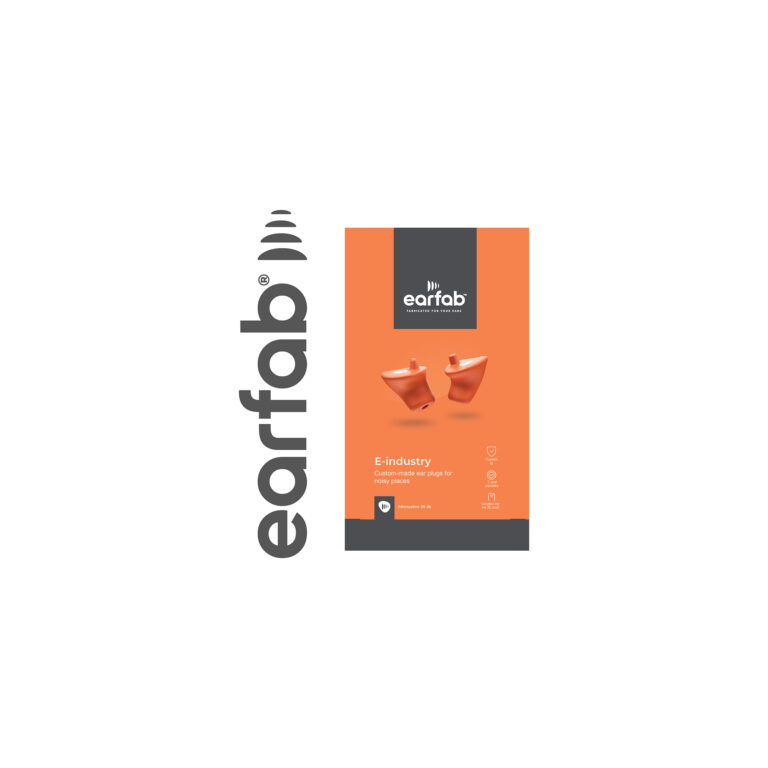